Revolutionizing Success: Navigating the Imperative of Process Improvement in Business
by kent2
Posted on 01-10-2023 12:14 pm
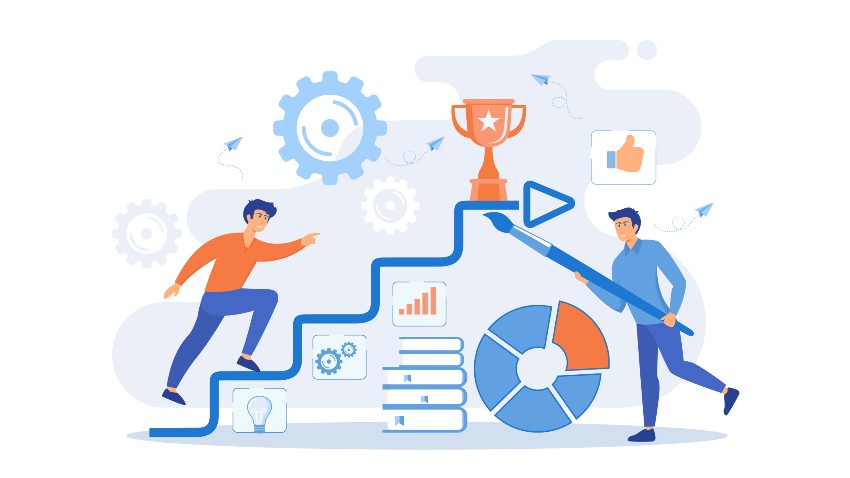
The Power of Process Improvement
In today's ever-evolving business landscape, process improvement isn't merely a buzzword; it's a strategic imperative. The ability to streamline operations, enhance quality, and boost productivity is the linchpin of sustainable success. Welcome to the first part of our journey through the world of process improvement – a journey that holds the promise of revolutionizing your approach to achieving goals and objectives.
The Importance of Process Improvement
Let's kick things off by understanding why process improvement matters now more than ever:
-
Competitive Advantage: In an era of cutthroat competition, those who optimize their processes gain a significant edge. Process improvement can be your secret weapon.
-
Efficiency Amplified: Imagine your organization operating like a well-oiled machine, where every task flows seamlessly. Process improvement is the conduit to make this a reality.
-
Resource Optimization: Wasted time and resources are the enemies of profitability. By identifying and eliminating inefficiencies, you can direct your resources to where they matter most.
-
Customer Satisfaction: In a world where customers have endless options, providing a consistently superior experience is non-negotiable. Process improvement aids in achieving this.
-
Adaptability: Change is the only constant in today's business world. An optimized process framework ensures you can adapt swiftly to evolving market dynamics.
The Urgency of Action
The urgency of embracing process improvement cannot be overstated. In a rapidly changing landscape, hesitation can be costly. Here are a few critical reasons why taking action now is imperative:
-
Market Disruption: Industries are being disrupted at an unprecedented pace. Those who fail to adapt risk becoming obsolete.
-
Customer Expectations: Today's consumers demand more - quicker deliveries, better quality, and personalized experiences. Process improvement is your ticket to meeting these expectations.
-
Data-Driven Insights: We now have access to more data than ever before. Process improvement leverages this data to make informed decisions and predictions.
-
Globalization: With markets expanding globally, efficiency is no longer a luxury but a necessity. Streamlined processes can help you tap into new markets effectively.
-
Sustainability: As sustainability becomes a driving force in business, optimizing processes can help reduce waste and your environmental footprint.
What Lies Ahead
In the sections that follow, we will delve deeper into the world of process improvement. We will uncover the key strategies and methodologies that can transform your operations. From Lean principles that focus on eliminating waste to Agile methodologies that embrace change, we'll leave no stone unturned.
So, are you ready to embark on this transformative journey? In the next section, we will demystify the core concepts of process improvement. Let's unravel the secrets to enhancing your efficiency and achieving immediate results.
Next: Decoding Process Improvement
Stay tuned as we dive into the heart of process improvement in the upcoming section. We'll define its core principles, explore its role in enhancing efficiency, and share real-world examples of organizations that have reaped the benefits. Your path to revolutionizing success continues.
Stay ahead of the competition. Explore the world of process improvement today!
Decoding Process Improvement
In the quest to revolutionize your success, understanding the core concepts of process improvement is essential. In this section, we will embark on a journey to decode the intricacies of process improvement, shedding light on its principles, functions, and the real-world impact it can have.
Defining Process Improvement
At its essence, process improvement is a systematic approach aimed at making processes more efficient, effective, and adaptable. It involves a series of actions and strategies designed to optimize workflows, reduce waste, and enhance the quality of outcomes. But let's break it down further:
-
Efficiency: Process improvement strives to streamline operations, ensuring tasks are completed with the least amount of time, effort, and resources. This translates into cost savings and faster delivery.
-
Effectiveness: It's not just about doing things faster but also doing them better. Process improvement focuses on achieving desired outcomes with precision and consistency.
-
Adaptability: In a world where change is constant, adaptable processes are key. Process improvement methodologies equip organizations to pivot quickly in response to evolving circumstances.
The Core Principles
To grasp the essence of process improvement, it's crucial to acquaint ourselves with its core principles:
-
Customer-Centricity: The customer is at the heart of process improvement. Every change made aims to enhance customer satisfaction and meet their evolving needs.
-
Data-Driven Decisions: In the world of process improvement, data reigns supreme. Data analysis and metrics guide decision-making, helping organizations identify areas for improvement.
-
Continuous Improvement: Process improvement isn't a one-time event but a continuous journey. Organizations are encouraged to constantly assess and enhance their processes.
-
Team Collaboration: It's a team effort. Employees at all levels are involved in identifying, analyzing, and implementing process improvements. Their insights are invaluable.
The Role of Process Improvement
Now that we've defined process improvement and its core principles, let's explore its pivotal role in the business world:
-
Cost Reduction: By eliminating waste and inefficiencies, organizations can significantly cut costs, enhancing their bottom line.
-
Quality Enhancement: Quality is non-negotiable. Process improvement ensures products and services consistently meet or exceed customer expectations.
-
Resource Optimization: Resources are finite. Process improvement helps organizations make the most of their people, time, and materials.
-
Competitive Edge: In a crowded marketplace, the ability to deliver better products or services, faster and more cost-effectively, is a distinct competitive advantage.
-
Compliance and Risk Management: Some industries require strict adherence to regulations. Process improvement aids in compliance and mitigating risks.
Real-World Success Stories
To truly appreciate the impact of process improvement, let's look at some real-world examples:
-
Toyota's Lean Manufacturing: Toyota revolutionized the automotive industry by implementing Lean principles, reducing waste, and optimizing production.
-
Amazon's Fulfillment Centers: Amazon's commitment to process improvement is evident in its highly efficient fulfillment centers, enabling swift deliveries.
-
Healthcare Efficiency: Hospitals worldwide have embraced process improvement to reduce patient wait times, improve care quality, and enhance patient experiences.
What's Next?
As we conclude this section on process improvement, we've gained a fundamental understanding of its definition, principles, and role in business success. But we've only scratched the surface. In the next section, we'll dive deeper into the actionable strategies and methodologies that can bring about tangible improvements in your processes.
So, if you're ready to take the next step on your journey to revolutionizing success, let's explore the 7 urgent process improvement strategies that promise immediate results.
Unlock the power of process improvement. The journey continues.
The 7 Urgent Process Improvement Strategies
Welcome to the heart of our journey to revolutionize success through process improvement. In this section, we'll explore seven urgent process improvement strategies that have the potential to bring about immediate and transformative results. These strategies are tried, tested, and adopted by leading organizations worldwide.
Strategy 1: Lean Principles for Streamlining
Lean principles are all about maximizing value while minimizing waste. Here's a closer look at how Lean can revolutionize your processes:
-
Identification of Waste: Lean helps identify and eliminate eight types of waste, including overproduction, waiting, and defects.
-
Value Stream Mapping: This technique allows you to visualize the entire process, enabling targeted improvements.
-
Just-In-Time (JIT): JIT production ensures you produce only what's needed when it's needed, reducing excess inventory.
Strategy 2: Six Sigma for Quality Enhancement
Six Sigma is synonymous with quality improvement. Here's how it works:
-
Define-Measure-Analyze-Improve-Control (DMAIC): The DMAIC methodology provides a structured approach to problem-solving and process improvement.
-
Statistical Analysis: Six Sigma relies heavily on statistical tools to identify and reduce defects.
-
Certification Levels: Individuals can achieve different Six Sigma certification levels, from Green Belt to Black Belt, signifying their expertise.
Strategy 3: Agile Methodologies for Adaptability
Agile methodologies are perfect for organizations that need to adapt quickly. Key aspects include:
-
Scrum: Scrum is one of the most popular Agile frameworks, emphasizing iterative development and flexibility.
-
Kanban: Kanban visualizes workflows and limits work in progress to enhance efficiency.
-
Sprints: In Agile, work is organized into time-bound sprints, allowing teams to deliver value incrementally.
Strategy 4: Kaizen for Continuous Improvement
Kaizen, which means "continuous improvement" in Japanese, focuses on small, incremental changes:
-
Gemba Walks: Managers often perform Gemba walks to observe processes firsthand and identify areas for improvement.
-
Kaizen Events: These are short, intense bursts of improvement activity, often lasting a few days.
-
Employee Involvement: Kaizen encourages employees at all levels to participate in improvement efforts.
Strategy 5: Total Quality Management (TQM)
TQM is a holistic approach to improving quality throughout an organization:
-
Customer Focus: TQM places a strong emphasis on meeting or exceeding customer expectations.
-
Continuous Training: Employees receive continuous training to ensure they meet quality standards.
-
Process Mapping: TQM involves detailed process mapping and analysis to identify bottlenecks and inefficiencies.
Strategy 6: Automation and Technology Integration
In the digital age, automation and technology play a critical role in process improvement:
-
Robotic Process Automation (RPA): RPA automates repetitive tasks, reducing errors and cycle times.
-
Data Analytics: Advanced analytics help organizations derive insights and make data-driven decisions.
-
Cloud Solutions: Cloud technology offers scalability and flexibility, supporting process improvement efforts.
Strategy 7: Employee Empowerment and Engagement
Engaged employees are more likely to contribute to process improvement. Key aspects include:
-
Ownership: Employees take ownership of their work and processes, actively seeking ways to improve.
-
Open Communication: Organizations with a culture of open communication tend to be more innovative.
-
Recognition and Rewards: Acknowledging and rewarding employee contributions to process improvement fosters motivation.
Choosing the Right Strategy
Each of these strategies has its strengths, and the choice depends on your organization's specific needs and goals. Some may even choose to combine multiple strategies for a comprehensive approach. The key is to align your chosen strategy with your organization's culture and objectives.
Now, armed with knowledge about these strategies, you're ready to take the next step in your journey toward revolutionizing success through process improvement. In the upcoming section, we will guide you through the practical steps of implementing your chosen strategy.
Your path to success continues as we delve into the implementation of your chosen process improvement strategy.
Implementing Your Process Improvement Plan
Congratulations on reaching this pivotal stage of our journey to revolutionize success through process improvement. In this section, we'll guide you through the practical steps of implementing your chosen process improvement strategy. Whether you've opted for Lean, Six Sigma, Agile, Kaizen, TQM, automation, or employee engagement, the following guidelines will help you translate your strategy into tangible results.
Step 1: Define Clear Objectives
-
Objective Clarity: Clearly define what you aim to achieve with your chosen process improvement strategy. Are you looking to reduce defects, increase efficiency, or enhance customer satisfaction?
-
SMART Goals: Ensure your objectives are Specific, Measurable, Achievable, Relevant, and Time-bound (SMART).
Step 2: Assemble a Dedicated Team
-
Cross-Functional Teams: Form teams that include members from different departments or areas affected by the process.
-
Leadership Support: Ensure leadership support and involvement to overcome potential roadblocks.
Step 3: Analyze Current Processes
-
Process Mapping: Create detailed process maps to understand current workflows.
-
Identify Bottlenecks: Pinpoint bottlenecks, inefficiencies, and areas where improvements are most needed.
Step 4: Select Appropriate Tools
-
Lean Tools: If you're implementing Lean, use tools like Value Stream Mapping, 5S, and Kanban boards.
-
Six Sigma Tools: For Six Sigma, utilize tools such as Pareto Charts, Fishbone Diagrams, and Control Charts.
Step 5: Implement Changes
-
Pilot Testing: Start with a small-scale pilot to test proposed changes and gather data.
-
Iterative Approach: Embrace an iterative approach, making adjustments based on real-time feedback.
Step 6: Monitor and Measure Progress
-
Key Performance Indicators (KPIs): Define KPIs to track progress. These should align with your objectives.
-
Data Collection: Continuously collect and analyze data to identify trends and areas for further improvement.
Step 7: Communicate and Train
-
Communication Plan: Keep all stakeholders informed about the changes and their impact.
-
Training: Provide training to employees to ensure they can adapt to new processes effectively.
Step 8: Evaluate Results
-
Assess Outcomes: Evaluate the results against your defined objectives and KPIs.
-
Lessons Learned: Identify what worked well and where improvements are still needed.
Step 9: Scale Up
-
Expand Implementation: If the pilot proves successful, scale up the implementation across the organization.
-
Continuous Improvement: Continue to seek opportunities for refinement and optimization.
Step 10: Share Success Stories
-
Internal Promotion: Celebrate your successes internally to motivate and inspire your team.
-
Knowledge Sharing: Encourage sharing of best practices and lessons learned.
By following these steps, you'll be well on your way to realizing the full potential of your chosen process improvement strategy. Remember that process improvement is an ongoing journey, and the commitment to continuous improvement is what sets apart successful organizations.
Now, as we conclude this section on implementing your process improvement plan, let's prepare for the next phase. In the upcoming section, we will explore the immediate results that can be achieved by applying these strategies effectively.
Your path to revolutionizing success continues. Get ready to witness the transformation in the next section.
Achieving Immediate Results: The Fruits of Process Improvement
Welcome to the final leg of our journey to revolutionize success through process improvement. In this section, we will explore the tangible and immediate results that can be achieved by implementing the strategies and methodologies we've discussed so far. These results are not merely theoretical; they represent the real-world impact that process improvement can have on your organization's performance.
1. Cost Savings
One of the most immediate benefits of process improvement is cost savings. By identifying and eliminating inefficiencies, redundancies, and wasteful practices, you can significantly reduce operational costs. This translates into a healthier bottom line and increased profitability. Whether it's through Lean principles, automation, or other strategies, the dollars saved through process improvement can be substantial.
2. Enhanced Quality
Quality is paramount in today's competitive landscape. Process improvement strategies like Six Sigma and TQM are designed to elevate the quality of your products and services. Fewer defects, higher customer satisfaction, and reduced rework contribute to a reputation for excellence. Improved quality not only retains existing customers but also attracts new ones through positive word-of-mouth.
3. Increased Efficiency
Efficiency gains are perhaps the most noticeable and immediate results of process improvement. By optimizing workflows and eliminating bottlenecks, tasks are completed faster and with fewer resources. This increased efficiency can lead to quicker project delivery, reduced lead times, and improved customer responsiveness.
4. Enhanced Employee Satisfaction
Engaged and empowered employees are more likely to contribute their best efforts. Employee-centric process improvement strategies foster a sense of ownership and pride in their work. As a result, you'll see higher employee satisfaction, reduced turnover, and increased innovation as your workforce actively identifies and suggests improvements.
5. Better Adaptability to Change
In today's fast-paced business environment, adaptability is crucial. Agile methodologies, a key process improvement strategy, equip organizations to pivot quickly in response to changing market conditions. This adaptability ensures you remain competitive and can seize opportunities as they arise.
6. Competitive Advantage
As you implement process improvement strategies and witness immediate results, you gain a significant competitive advantage. Your ability to deliver higher quality products or services, at a lower cost, and with faster turnaround times sets you apart in the market. This competitive edge can lead to increased market share and sustained growth.
Conclusion: Your Path to Success
In this comprehensive journey, we've explored the power of process improvement from its definition to its implementation and the immediate results it can yield. Whether you choose Lean, Six Sigma, Agile, Kaizen, TQM, automation, or employee engagement, the key is to align your chosen strategy with your organization's unique goals and culture.
Process improvement is not a one-time event but an ongoing commitment to excellence. It's a journey that, when undertaken with dedication and a focus on continuous improvement, can revolutionize your success.
As we conclude this series, we encourage you to embark on your own process improvement journey. Implement the strategies that resonate most with your organization, and remember that the road to success is paved with continuous improvement.
Revolutionize your success through process improvement. Your journey begins now.
You can also check this link:
https://elink.io/p/business-process-improvement-967ca2b